Telecomms Manufacturer Opens Gem Of A Warehouse In Joburg
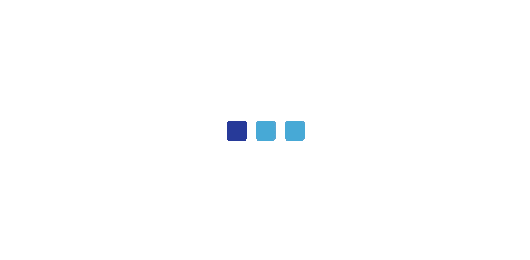
Huawei Technologies has opened a new warehousing facility, marketed as ideal for South Africas challenging conditions, based on focused design and dynamics summarised as GEM green energy, e-security and modern logistics.
The overall size of the premises in Linbro Park, between Sandton and OR Tambo International Airport, is 30000 square metres and it is equipped with the latest artificial intelligence AI in access control.
The warehousing capacity itself is 14000 sqm and, according to Stevin du Plessis, logistics manager for Huawei South Africas Supply Chain Business Department, is split in two the one warehouse being dedicated to in- and outbound tech movement and the other handling localised supplies and spare parts.
Huawei SAs chief executive, Will Meng, said great emphasis had been placed on the facilitys energy efficiency and, as such, it is equipped with the latest solar panelling tech.
But it is the facilitys premier warehouse, where five automated guided vehicles AGVs and three automated guided forklifts AGFs are on duty instead of an over-abundance of pickers, where Huawei believes the real magic is happening.
Du Plessis explained that, to secure automation requirements, the latest multiplicity tech in WiFi routing was in use, ruling out connectivity downtime.
In addition, about 60 cameras situated throughout the warehouse means there is no blind spot.
It also gives us a certain kind of AI functionality where we are able to identify certain things.
He said, for example, if there was human interference in the automated process of the warehouses stock arrangement and movement, the AI-driven security system of the warehouse could immediately flag it.
Its one of the reasons why this is a 100 accurate warehouse without any losses.
Thanks to the integration of seamless in- and outflow systems and the deployment of AGVs and AGFs, Huawei has increased human-error elimination, unnecessary picking movement through centralising stock replenishment and dispatch procedures, and decreased occupational hazard risks by limiting unnecessary human involvement.
The system understands what items are coming in, where is the best place to put it based on demand and frequency, and through grouping goods with similar items, ensures practical replenishment for fast and effective dispatch.
Officially, Huawai said the facilitys picking efficiency was between 60 and 110 line items per hour, thanks to the AGVs and AGFs, respectively capable of 600 kilograms and a tonne with each move.
When the machine batteries run low, they automatically go to recharge to avoid lithium-ion dips lower than 30 but, based on the required AI-assessed workload at the time, will recharge accordingly.
If its peak hour, for example, an AGV or AGF will recharge up to the level required to finish its workload before going for a full top-up.
Principal business and strategy consultant, Alvin Korkie, said through advanced AI methods, Huawei has been able to flip the proverbial script on traditional warehouse practice.
Whereas picking has always been based on persons-to-goods, we have been able to turn that around to goods-to-persons.
Thanks to the intelligence of the system, we know exactly what orders have been placed and, during downtime, pickers fetch replenishment stock for our machines to move into the respective areas of processing.
It drives down the overtime of hi-rack pickers by about 150 hours a month, saving time and cutting down on human fatigue.
Our solution isnt human-driven, Korkie said.
Its tech-driven.
Sign up to our mailing list and get daily news headlines and weekly features directly to your inbox free. Subscribe to receive print copies of Freight News Features to your door.